UNLEASH YOUR SHAPE
THE INFLATABLES OF
YOUR DREAMS ARE HERE
TECHNOLOGY
Our proprietary shapewave® robot welding technology enables us to manufacture structural inflatables with unparalleled freedom in shape and material options.
How it works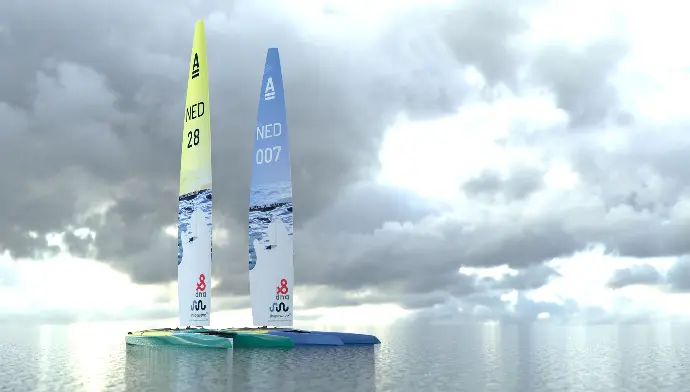
USE CASES
Imagine being able to 3D shape inflatable products exactly the way you want without complex tooling or high start up costs and you'll realize the possibilities are endless.
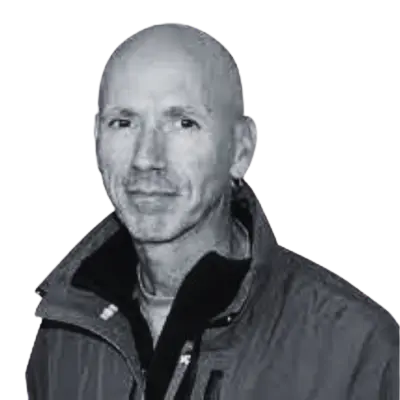
We dreamed of it for 30 years and you did it! Congratulations!
BRUNO LEGAIGNOUX
Inventor of LEI inflatable kites
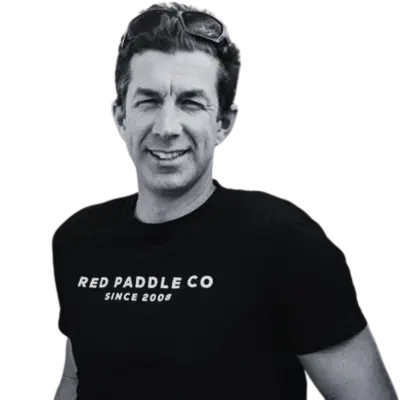
It's super exciting to be part of this project! Great work!
JOHN HIBBARD
Founder/ CEO Red Paddle Co
LIGHTWEIGHT
shapewave® technology uses coated fabrics available airtight from the roll, for use in ultra light to heavy duty constructions. Each of the thousands of individually welded tapes inside your shapewave® inflatable is precision calculated in accordance with physics laws via our specially created WAM (Webbing Allocation Module) software for an optimised construction.
Our ultralight proprietary tape material barely adds to the construction weight. At the lightest of light, shapewave® can provide construction weights of 100gr/m² for ram-air canopies as an example. Weight savings of over 60% compared to traditional inflatable manufacturing technologies are well within reach.
FREEDOM OF SHAPE
Liberate your designs from tubular, flat panel or box confinement as you tap in to the world of shapewave® possibilities! Double curvature, sharp edges*, convex or concave, our proprietary WAM software will take your design and fill it with the required tape density, ensuring specific weld placement to create shape and providing panel join lines to build the inflatable parts you have been dreaming of. Think of nose and tail rockers on a surfboard which are simply not possible with current forms of inflatable product manufacturing such as drop stitching.
*Current minimum radius is R18mm. Note that thin sections of inflatables can become "soft" due to reduced hoop stress. Blame physics! However, sharper edges can be achieved by other means, please contact us directly for details.
GREENER
Most of the materials we use are fully recyclable and can be substituted to some extent by biobased materials; an even greener future that we are eager to explore!
Our processes are fully electric and do not require consumables or toxic resins. Surplus material (cutting waste) is collected by our suppliers. Our shapewave® farms run entirely on green electricity. shapewave Industries BV is working towards B Corp. Certification as soon as possible.
LIGHTWEIGHT
shapewave® technology uses coated fabrics available airtight from the roll, for use in constructions from ultra light to heavy duty. Each of the thousands of webs inside your shapewave® inflatable is precision calculated in accordance with physics laws by our WAM software for an optimised construction.
Our ultralight proprietary tape material hardly adds to the construction weight. Weight savings of over 60% compared to traditional inflatable tech are within reach. At the lightest of light, we're looking at construction weights south of 100gr/m² for ram-air canopies.
FREEDOM OF SHAPE
Liberate your designs from tubular, flat panel or box confinement as you tap in to the world of shapewave®! Double curvature, sharp edges*, convex or concave, our proprietary WAM software will fill your design out with the required tape density, while providing panel join lines to build the inflatable parts you've been dreaming of.
*Current minimum radius is R18mm. Note that thin sections of inflatables can become "soft" due to reduced hoop stress. Blame physics! However, sharper edges can be achieved by other means, please contact us for details.
GREENER
Most of the materials we use are fully recyclable and can be substituted to some extent by biobased materials; an even greener future that we are eager to explore!
Our processes are fully electric and do not require consumables or toxic resins. Surplus material (cutting waste) is collected by our suppliers. Our shapewave® farms run entirely on green electricity. shapewave Industries BV sets out to be accredited as B corp. as soon as possible
Licenses available
contact us to discuss the options.
First sample products built
We're building the first samples for actual customers to perform field testing.
Ready for you!
We're ready to start designing and testing the first shapewave® applications!
wavemaker01
First wavemaker assembled and ready for testing.
Attending METS
The METS participation 2023 turned out to be a great success, bringing many new leads, markets and applications